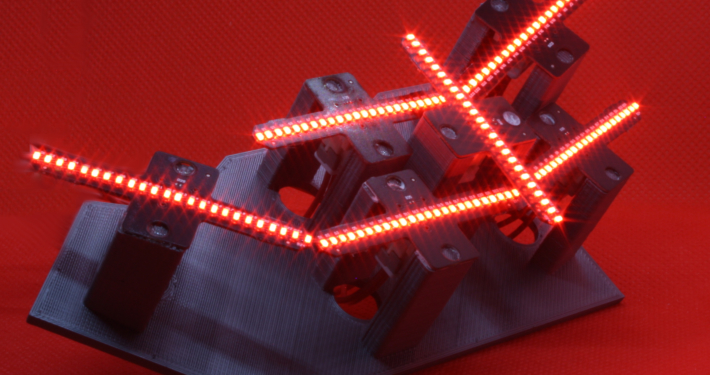
There is hardly any industry that places such high demands on its technology suppliers as the automotive industry. Many car manufacturers and set makers have been relying on vosla for many years. And that has a good reason.
The technical requirements are as challenging in the automotive industry as hardly anywhere else. We talked to Jörg Hochmuth about how vosla faces up to this challenge. Hochmuth is Head of Production Department at vosla.
Carsten Teller (Exacton editor): Mr. Hochmuth, could one say that automotive lamps are something of the royal class in this field?
Jörg Hochmuth (vosla): In any case, that’s easy to say. In addition to the aircraft industry, the car manufacturers and set makers who supply them are the ones with the strictest specifications. You see, we have to meet standards that comply with industry standards. We have them certified regularly. There are also various special requirements for special requests and individual solutions. Our answer to this is always the same: We exceed standards and standards with very precise measurements and quality controls at every step of the production line.
Carsten Teller: Could this be exactly numbered?
Jörg Hochmuth: Our measuring systems are so accurate that we can measure deviations in the range of a hundredth of a millimeter. Assuming that the required manufacturing tolerance is one or two tenths of a millimeter, then we exceed these requirements tenfold. We document all this completely for every single lamp, even at a production rate of 4,000 per hour.
Carsten Teller: That sounds almost pedantic.
Jörg Hochmuth: We even go one step further, and I think that’s unique in the market: We document all production values and geometry data except for the second of production with a QR code, which we finally apply to each lamp. It’s like a signature for every single lamp. We are currently looking at ways to encrypt additional data and information about the product on customer request – this is a unique added value for the customer and makes every production step traceable. But the heart of the matter is the exact documentation of quality assurance.
Carsten Teller: You can only ensure that if you manufacture each lamp component yourself.
Jörg Hochmuth: That’s the way it is. That’s why we also manufacture almost every component of the burner manufacturing process chain ourselves. An exception are glass tubes. We do not produce these ourselves, but process them further to our requirements and specifications. What matters in the end, however, is the experience and competence that we have had in our factory for decades. For other components, third-party manufacturers must work to our design specifications and meet our stringent specifications. In the end it is then so that we only process things that were developed in our house, excluding raw materials.
Carsten Teller: vosla has a certain tradition of producing very special lamps. These include signal lamps or those for special vehicles and construction vehicles. Has the car lighting also remained specialized?
Jörg Hochmuth: The specialization lies in the fact that we deliver everything that has to meet extremely high requirements, and that is only reliable and deliverable with our claim to the highest possible precision. In the automotive sector, this includes the entire line from HB3 to HB4, respectively for high and low beam and also efficiency enhancing in-house developments such as the HIR2H, which combines both in one lamp. In addition there are H8, H9, H11 and the specialization on the particularly robust requirements of trucks.
Carsten Teller: Why can you truck?
Jörg Hochmuth: We bring decades of expertise for special vehicles and construction machinery. When we talk about the truck segment, we are essentially talking about 24 volt lamps. But this is not just about the higher voltage. If you think about construction equipment alone, then you can imagine what kind of robustness is required. And it’s not just about the tension, but also about completely different helix, as we need it in the normal automotive sector. That’s where we talk about twin helix technology. This is, simply put, a wire wrapped around another wire.
Carsten Teller: Why do you need double helix in the truck sector? For normal cars you also make extremely bright lamps, the H3 or H7, for example. And these are single coils.
Jörg Hochmuth: The brightness is not the point. Trucks, for example, are operated with 24 volt on-board voltage. But you can not do that with single coils. Even the wire thicknesses with a simple tungsten wire do not stand up to it. They burn through you. That is, you can not guarantee the demands on durability and reliability with single-coils. For this you absolutely need double helix technology – this is the measure of all things.
Carsten Teller: Added to that is the vibration and shock resistance in the truck sector.
Jörg Hochmuth: There are a number of international standards that we have to meet in order to obtain the necessary certifications in each country. They are Bulb Deflection tests, but also vibration tests and others. We have labs and test tracks for all these tests. These include lighting, performance and durability tests. All our lamps are cyclically subjected to these tests. Some equipment is also booked by other scientific institutes if we have spare capacity.
Carsten Teller: Not only at scientific institutes you have a good name for your work – apparently also with your competitors.
Jörg Hochmuth: Right, that’s the way it is. In this case, competition also enlivens our business. I’ll say it metaphorically: If the global players, I do not want to name names now, the lights go out, then go to vosla. In automotive lighting, we create up to 32,000 halogen lamps per day with our 4.000 series. All made with the same precision. This means that we can cover every production bottleneck of our competitors without hesitation. And we do that regularly.
Carsten Teller: As a specialist for the automotive industry, vosla ensures extremely tight production tolerances and therefore perfect light for set makers and car makes directly. Who benefits from your claim to perfection?
Jörg Hochmuth: We also supply the premium segment of spare parts dealers and therefore also workshops. They are also happy to recommend a superior product with a clear conscience. In the end, the customer always wins.
Carsten Teller: Mr. Hochmuth, thank you very much for this interview.