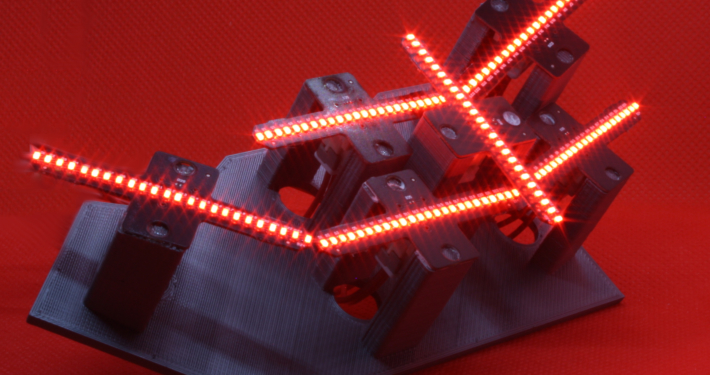
vosla celebrates its 70th anniversary in 2018 – a barely imaginable time span in a highly competitive sector such as lamp production! How could that succeed? And: How can one keep a distance from international competition in times of globalization? We talked to managers for product marketing Bernd Müller and Ron Orlamünder, responsible for industrial engineering and CIP production.
The Saxon Plauen has invented itself over the course of history again and again: In the Middle Ages trading center, from the 18th century important location of the Saxon textile industry, at the latest from 1920 the center of mechanical engineering and manufacturing. Despite numerous crises and socio-political changes: To this day, the people here have remained true to their special craft and Tüftlerkunst.
This enthusiasm for innovation also shaped the company vosla right from the start. But how does one convert this enthusiasm into market success in the long term? For the production of lamps for special applications in the high-end areas of automotive, railway, aviation and medical technology, this requires, in addition to perseverance, above all a lot of creativity, flexibility and precision. Because in this industry survives only who is willing to respond to changing market requirements very flexible.
“The technologies and products are changing,” says Bernd Müller. “But what remains is the customer’s desire to be able to offer or use the most attractive product in the competition.” And Ron Orlamünder adds: “That’s exactly what drives us time and time again. Whether on the OEM market for original equipment manufacturers or the aftermarket, ie the aftermarket. Our aim is always to further expand our market access with innovative and significantly improved products. ”
Creative Development Needs Interdisciplinary Teams
The manufacture of lamps is technologically demanding. “You can not learn it theoretically,” Orlamünder explains. “Years of experience on site in production practice are indispensable.” Creativity always means both improvements to the products and to the production process: this is the only way to achieve cost savings and at the same time guarantee the highest product quality. That is why programmers and electronics engineers have long been strengthening the vosla team.
High-quality image processing systems ensure the ultra-precise geometric measurement of all lamp modules at every single production step as well as the meticulous acquisition of the acquired data. As a result, vosla achieves an unprecedented level of quality and production.
From 1974, the company developed the headlight bulb H4 using quartz glass. The next innovation step was their production from the end of the 70s with tempered glass. “We were the only ones in the world who designed this lamp so that a wire bridge, instead of a quartz beam, holds the electrodes together,” says Orlamünder. “Within the production process, this wire bridge was then electrically blown to prevent short circuits. The biggest advantage: Simplification of the production process and associated cost advantages, which could then be passed on to customers. The H4 should prove to be one of the company’s key products. It was manufactured until 2010.
A car that turns a blind eye
“The effect resulted from the interaction of our lamp with a bundle of optical cables, which scatter the light in a ring,” explains Müller. “We are the only company in the world to supply this lamp. It is no longer produced today for the original equipment manufacturer, but still for the aftermarket. “The H10 W also impressed with its outstanding service life of 2200 hours. It therefore fulfilled all requirements perfectly.
Not infrequently, these are problems that drive the engineers and technicians at vosla to particularly innovative developments. In a special headlamp application, the soldered ground contact proved problematic because the solder began to melt at 210 degrees. For this reason, from 2009, vosla developed the H21W HTR for the Audi Q7 – a high-temperature-resistant lamp with welded instead of soldered ground contact. Manufactured using the innovative laser welding process, the H21W HTR managed to withstand almost unthinkable temperatures of up to 300 ° C without damage.
The orange revolution
In 2008, vosla achieved another masterpiece: the automotive industry was thirsting for innovative designs around the lighting elements on vehicles. The world’s first development was the creation of the HY21W, a halogen miniature lamp for flash applications. It is one of the “other-colored” lamps, donates intense yellow-orange light and shocked the competition with its small dimensions compared to conventional lamps doubled life.
Thanks to the HY21W, car manufacturers were able to equip their vehicles with clear-glass lenses instead of the usual orange turn signal covers worldwide – for many, this was equivalent to an optical revolution.
The hard glass bulb is coated in orange on the HY21W by a dipping process. What sounds so simple was quite a headache for the developers in the experimental phase: The halogen miniature lamp produces a very high bulb temperature of up to 400 degrees Celsius. It therefore needed a novel, color-exactly defined and long-term high temperature resistant color coating. It was necessary to precisely meet the tight regulatory requirements of the Federal Motor Transport Authority and TÜV, described by the coordinates X and Y in the color triangle of red blue and green, the “CIE color space”.
vosla managed to reconcile long-term color accuracy, attractive lamp life and, last but not least, the market-driven pricing of the finished luminaire in series production. Even today Vosla distributes the HY21W successfully and worldwide. Good for vosla, but also good for large customers, who enjoy many years of good profits and decades of safe production.
Modify, diversify – and minimize costs!
Automotive lamps that change the rules
Creativity in tight markets also includes the ability to modify novel product ideas based on a thorough understanding of market needs and consumer needs. In 2013, vosla developed the HIR2, a halogen headlamp for bi-halogen systems, for the automotive industry. The special thing about it: It combines the dipped and main beam functions in one lamp. “We were not the first to do so,” says Müller, “but we put the lamp on the market in tempered glass instead of quartz glass.” The advantage: the processing temperature during lamp production is significantly lower. Due to the lower energy consumption, vosla also achieved cost advantages for its customers. “We also offer the largest portfolio and the highest variety of types in HIR2,” says Müller. “These include the types ‘standard’, ‘longlife’, ‘+30’ with increased light emission and a blue lamp.”
At the futureSAX Innovation Forum in Plauen on October 27, 2015, vosla also showed how innovative power works – as one of the few selected Saxon companies to speak on this topic. The audience was impressed. Innovation today works best in the field of tension of superior product characteristics, almost radical quality management and low prices.
Today, under the NARVA and vosla brand names, vosla offers its customers no less than 500 different special lamps and over 100 different types of automotive lamps. And how does it continue? “Of course with a lot of innovation, Orlamünder smiles. “We can not help it. We’re burning for light! ”